- 22 Jul 2024
- 6 Minutes to read
What can I do with FLACS?
- Updated on 22 Jul 2024
- 6 Minutes to read
What can I do with FLACS?
FLACS is a specialised process safety tool, designed to help safety engineers assess the potential consequences of accident scenarios. It offers a number of simulation types that can be applied across a wide range of scenarios including:
Dispersion
Gas explosion
Dust explosion
Fire
Blast
FLACS and its various solvers can be applied to any market or industry, including emerging fields such as renewable technologies, hydrogen production facilities and refuelling stations, biomass power plants, and battery energy storage system (BESS) facilities.
Dispersion
The dispersion solver allows users to model releases of gas or flashing liquids and their subsequent dispersion, both internally and externally. Dispersion simulations in FLACS account for interactions with complex geometries, enabling entire facilities and the surrounding areas, including terrain, to be captured in the model. Both natural and mechanical ventilation can be applied, and ventilation-only scenarios can also be conducted when a leak is not defined.
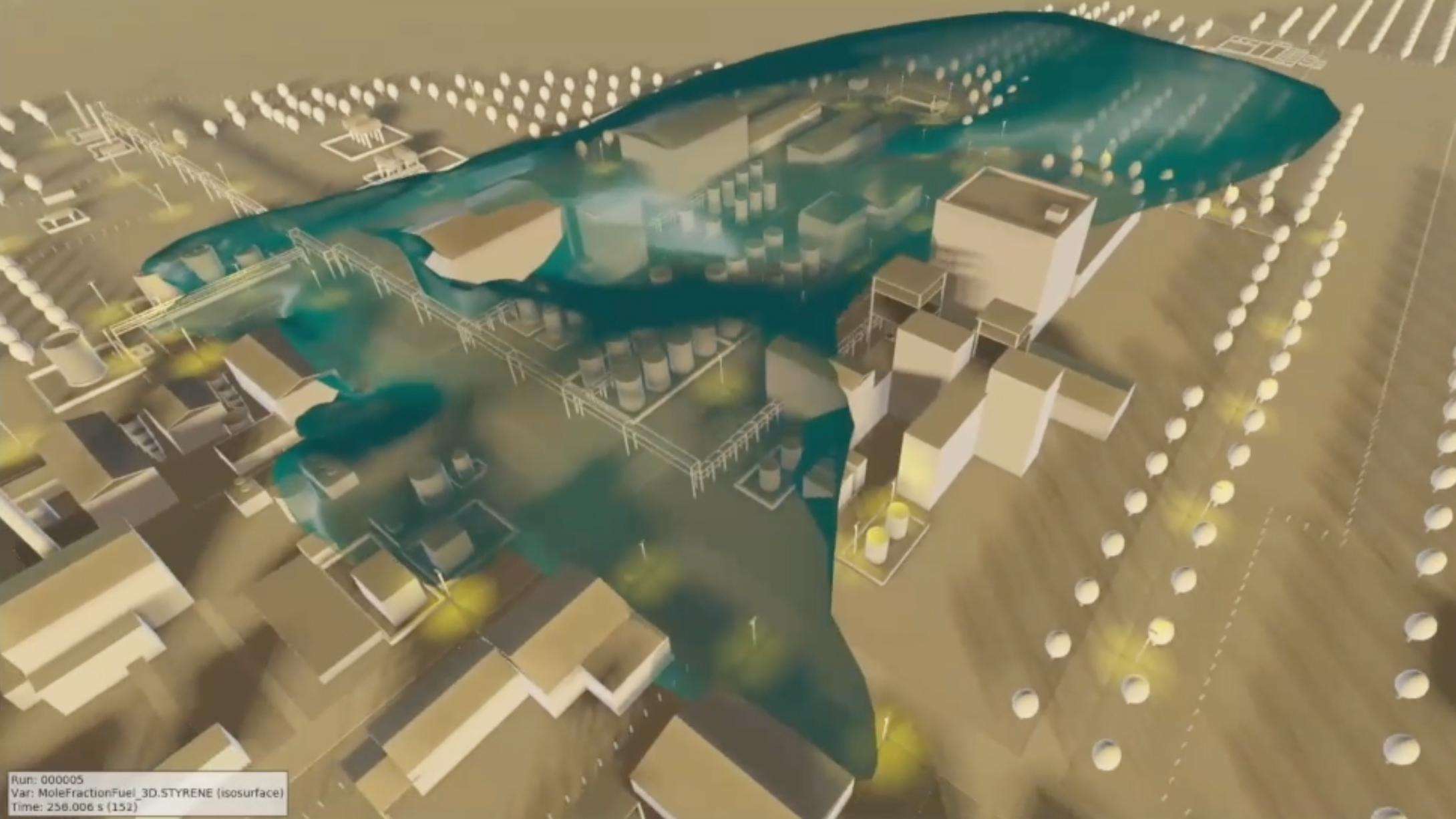
FLACS uses the DIPPR database, which enables the use of a wide variety of materials, including flammable, toxic, and asphyxiant gases.
Results from flammable gas dispersion modelling can determine the maximum extent of gas clouds relative to flammable limits, gas concentrations at critical areas (e.g., around potential ignition sources), and the flammable cloud volume. These results can also be used as inputs into gas explosion simulations.
Modelling toxic releases can determine whether populations could be exposed to high concentrations of toxic gases. Additionally, the toxic dose can be determined, accounting for the duration of exposure.
FLACS can be used to assess the effectiveness of mitigation measures and aid in their design. Ventilation arrangements can be assessed to determine whether the design is sufficient to mitigate the accumulation of gas following a release. Detection and isolation measures can also be assessed using a combination of monitor points and .EVENTS files.
When modelling a release, the leak wizard enables users to input various release parameters such as pressure, outlet size, temperature, releasable inventory, duration, and release rate. This functionality covers a wide range of release scenarios, from pinhole leaks to full-bore ruptures and releases from relief vents.
Additionally, the pool model in FLACS can be used to simulate liquid spills on the ground or water. Users can define spreading or static pools, or determine the pool by defining a leak. Static pools can model accidental releases confined by a bunded area or open vessels in processing plants. Spreading pools account for local geometry and topography. The evaporation rate of the pool is determined by several user-influenced parameters, including heat from the ground, flow above the pool, and radiation from the sun or fire.
The pool model accommodates toxic or flammable materials from the DIPPR database and is suitable for liquified gases and liquids below their flash points. Pool evaporation and subsequent dispersion can be modelled to determine the maximum extent of the resulting gas cloud and its concentration in critical areas.
Suitable scenarios for the pool model include:
Accidental release of LNG from a storage vessel
Vapour generation from an open-process vessel
Gas explosion
FLACS-GasEx, the FLACS explosion modelling solver, is used to simulate vapour cloud explosions. It helps analyse the consequences of explosions in industry and assess associated mitigation measures to minimise potential risks. Gas explosion simulations enable users to visualise the development of an explosion and its impact on surrounding structures, equipment, and personnel.
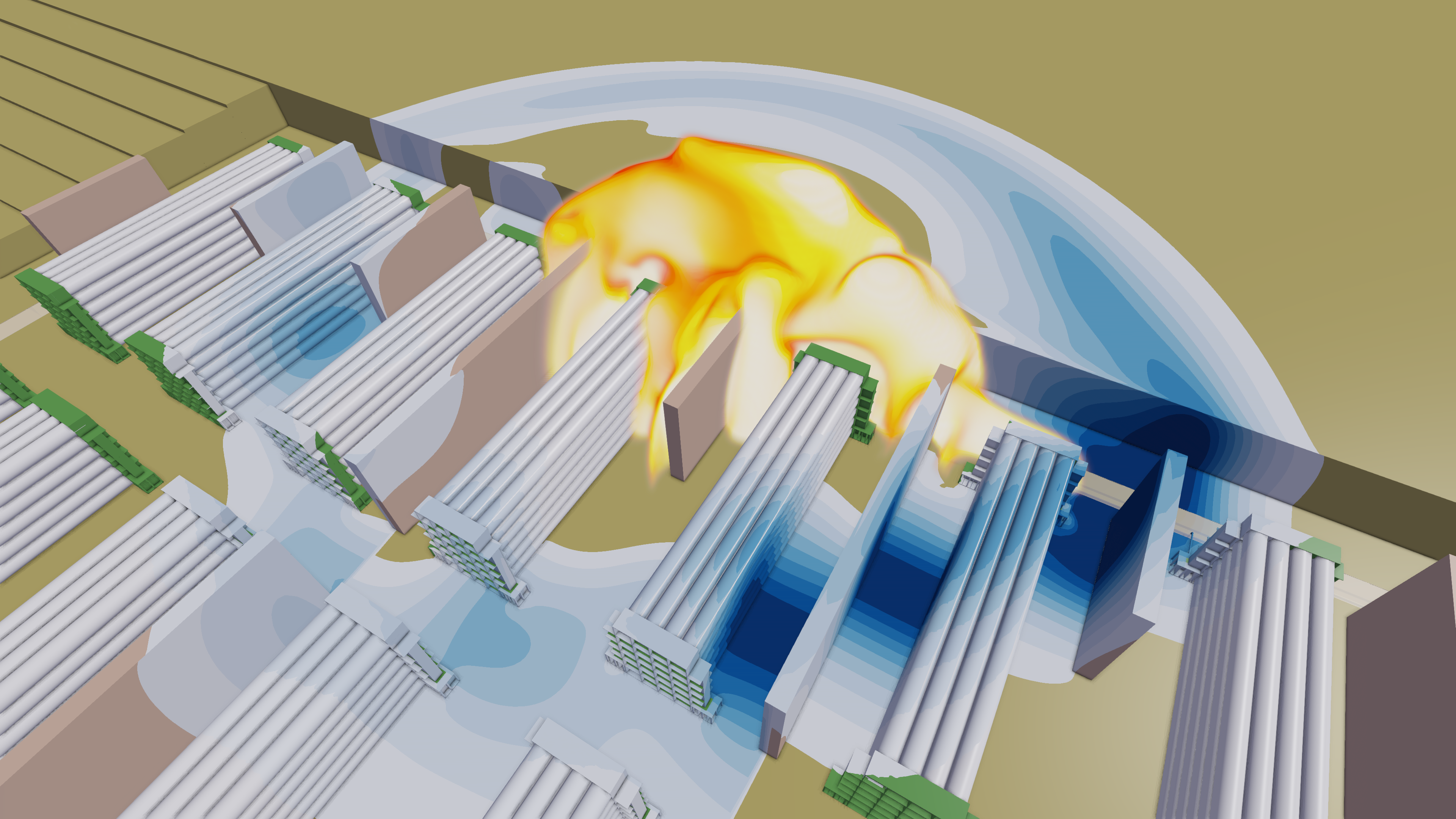
FLACS-GasEx models the positive feedback loop between expansion-generated flow and the increased rate of turbulent combustion, leading to flame acceleration, pressure build-up, and blast wave generation. It takes into account the interaction of the explosion with congestion and confinement through the geometrical model.
Recent developments allow users to model detonations and detonation to deflagration transitions (DDT). For hydrogen explosions, the detonation model activates automatically when the normalised pressure gradient surpasses a threshold limit.
FLACS-GasEx allows users to assess explosion consequences by predicting overpressures, pressure impulse, flame extent, and radiation levels in critical areas such as where people or sensitive equipment are present. Simulation results can inform equipment locations, facility siting, placement of blast walls, exclusion zones, and other mitigation measures such as deluge and pressure relief panels.
Various parameters, including gas compositions, concentrations, cloud volumes, cloud locations, and ignition locations, can be input into simulations to generate comprehensive results spanning potential real-world scenarios.
Examples of explosion modelling applications include:
Hydrogen refuelling stations and production facilities
Oil and gas platforms
Leaks from gas storage tanks
Chemical processing plants
Battery energy storage systems
Dust explosion
FLACS-DustEx, an extension of the FLACS tool, is specifically designed to model dust explosions in complex geometries. It assists in assessing potential dust explosion consequences, producing detailed three-dimensional pressure wave development and flame propagation plots and videos to clearly communicate explosion outcomes.
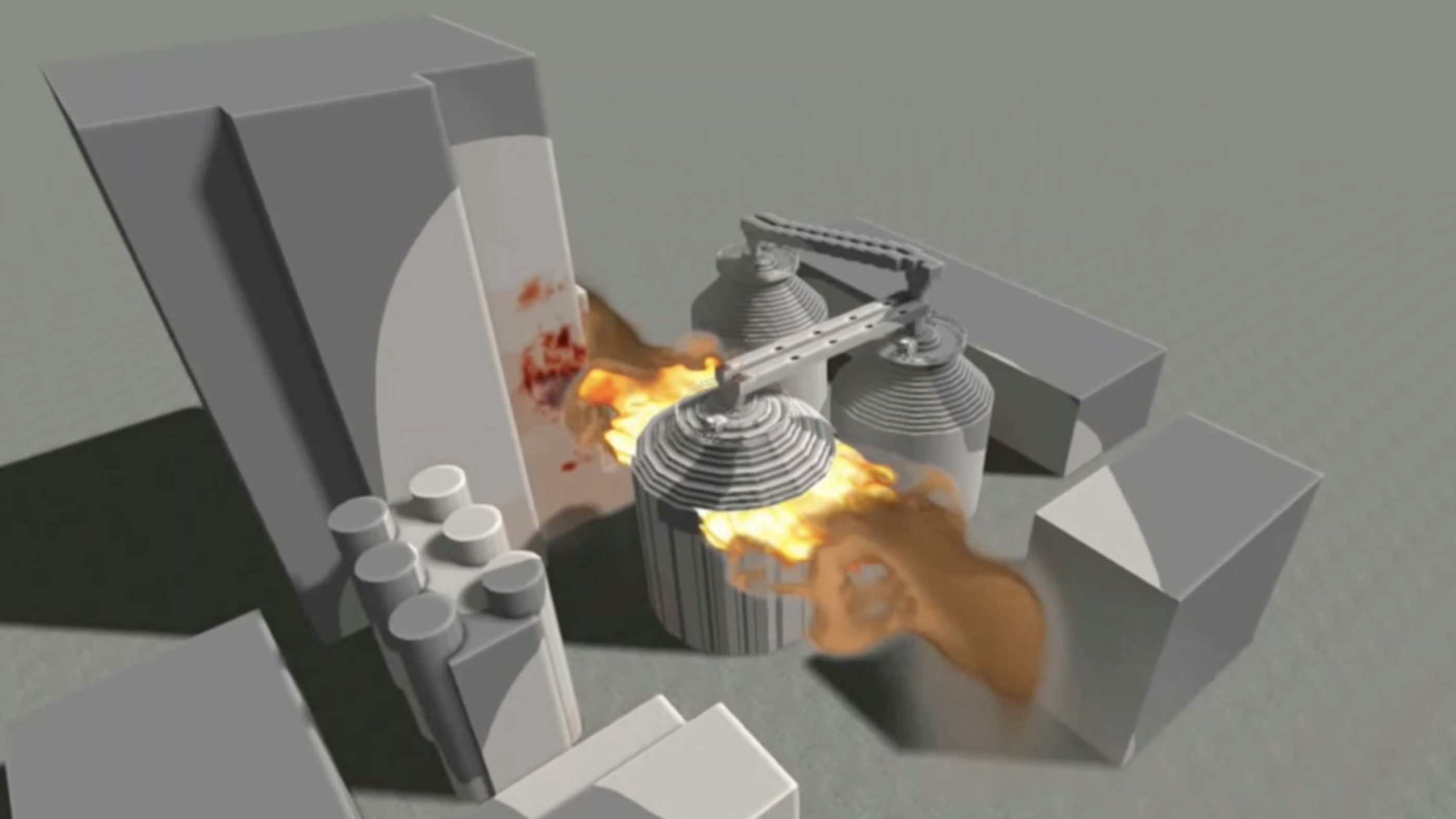
Users can input various parameters, including dust type, dust concentration, dust cloud size, and ignition locations.
FLACS-DustEx studies can assess:
Design pressure vs maximum pressure and/or maximum reduced pressure of equipment
Overpressures at nearby structures
Location of exclusion zones surrounding equipment or explosion relief vents
Effectiveness of explosion detection, protection, isolation, and suppression systems
Explosion venting requirements (assessing different opening pressures, arrangements, sizes, types, and number of relief vents)
FLACS-DustEx can be applied to various facilities and equipment such as bulk storage and transfer equipment (e.g., bucket elevators and conveyors), extraction systems and dust filters, and processing equipment (e.g., spray dryers and mills).
It is suitable for scenarios that cannot be adequately assessed using standard-based calculations, such as when dust explosion properties or vessel dimensions are outside the stated range, or when internal equipment configurations have turbulence-inducing elements along the explosion relief path.
As with all FLACS solvers, DustEx also considers interactions with geometries internally and externally, providing detailed pressure contour maps to assess potential damage. Dust explosion studies can also consider less conservative and more realistic scenarios, such as partially filled equipment or sub-stoichiometric dust concentrations.
FLACS-DustEx can model any organic dust, given available dust testing data (non-organic dusts, such as metal dusts, cannot currently be modelled in FLACS).
Fire
FLACS-Fire models jet and pool fires following a release from process equipment for various scenarios, including indoor and outdoor releases. It considers interactions between turbulent flow, buoyancy, convection, entrainment of air, soot formation, thermal radiation, fluid-structure interaction, dispersion of smoke, and toxic combustion products.
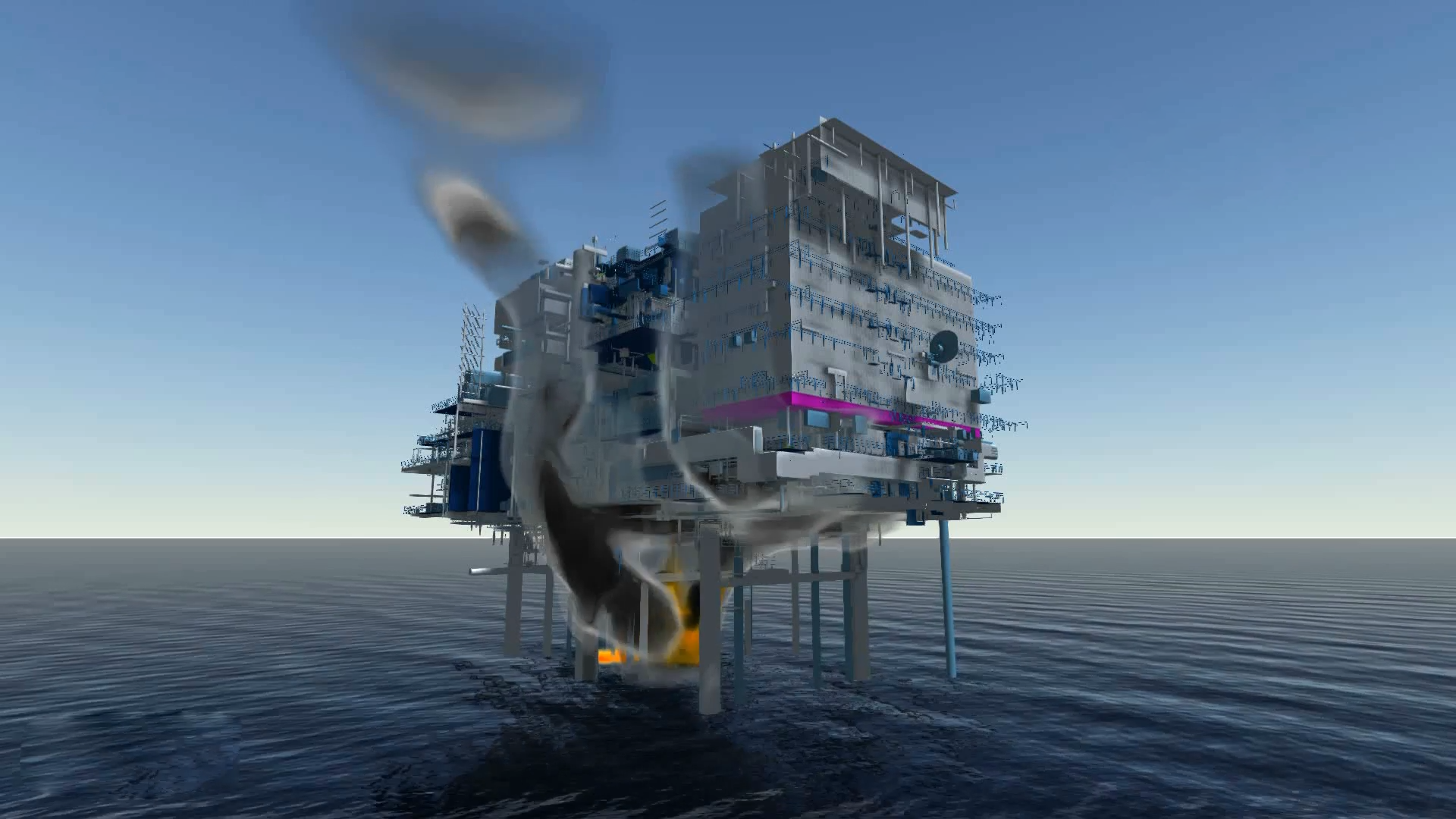
The solver models combustion primarily using the Eddy Dissipation Concept (EDC). Radiation is modelled using the Discrete Transfer Method (DTM) (recommended) or the six-flux model (simple model).
FLACS-Fire allows users to assess fire extent and subsequent impacts on equipment, structures, and people. Users can view results based on flames, temperature, radiation, and thermal dose, among others. FLACS-Fire simulations can also model pollutant emissions and soot/smoke generation.
Additionally, FLACS-Fire can model impinging jet fires, where equipment and structures provide shielding effects, potentially leading to less conservative results compared to simpler tools. This also allows users to include firewalls in the geometrical model to assess their effectiveness.
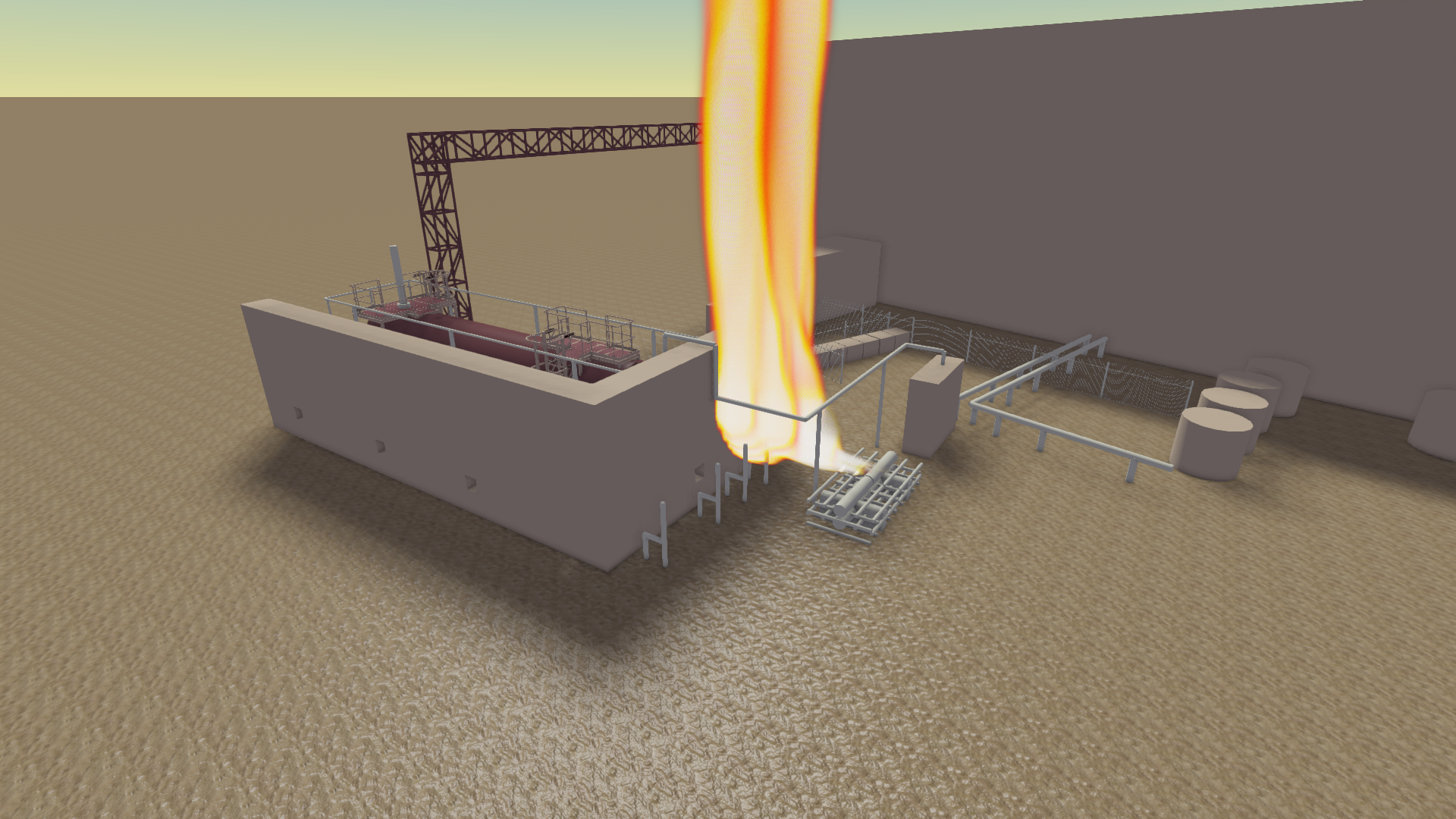
Users can define a leak similarly to a dispersion scenario, based on the same underlying release models. Liquid releases, subsequent pool formations, and flammable vapour generation can be modelled by defining a pool leak. The pool model can simulate liquid spills on the ground or water, considering local geometry and topography. Pool evaporation and subsequent dispersion can determine the maximum extent of the resulting gas cloud and its concentration in critical areas. Alternatively, a pool fire can be modelled by igniting the flammable vapours generated.
Example scenarios for FLACS-Fire and the integrated pool model include:
Release from LNG storage tanks and subsequent pool fire
Jet fire from accidental release at a hydrogen refuelling station
Flare on an oil and gas processing facility
Blast
FLACS-Blast simulates the propagation of blast waves from the detonation of condensed explosives. It can be applied to security applications or other high-explosive scenarios, such as those similar to the 2020 Beirut explosion.
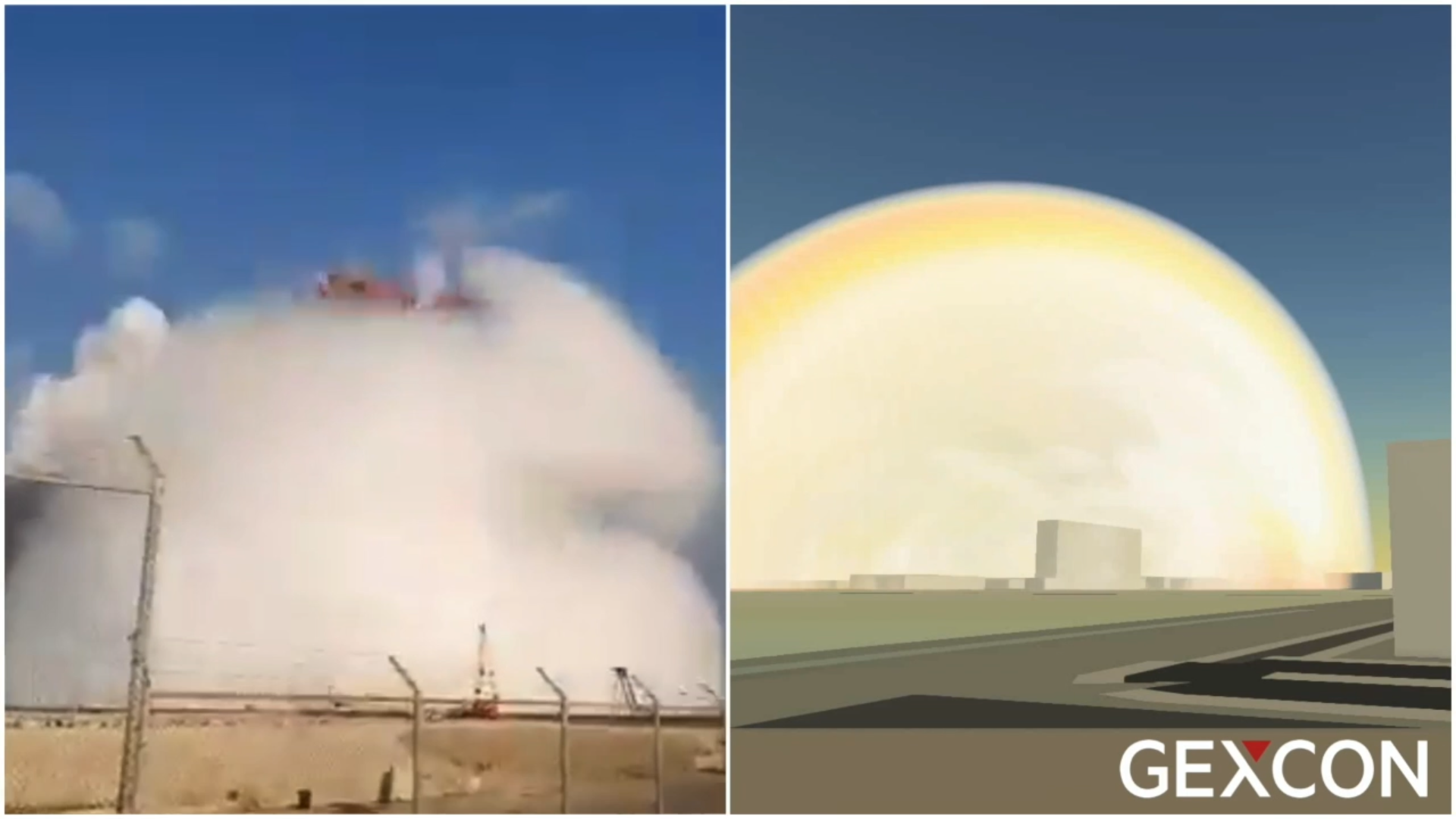
FLACS-Blast can model TNT or RDX directly and also offers the option to define a custom high-temperature, high-pressure region. Other materials can be modelled by converting them into a TNT equivalent mass.
Users can define a charge location, mass, and explosive type, as well as the direction of propagation. Simulation results can then be used to track blast overpressures throughout the domain, comparing them against damage criteria to assess blast consequences.