- 23 Oct 2024
- 5 Minutes to read
Simulating hydrogen jet fire
- Updated on 23 Oct 2024
- 5 Minutes to read
What is a Jet Fire?
Jet Fire at hydrogen refuelling stations can occur when pressurized hydrogen gas leaks, forming a flammable mixture with air that directly ignites. Hydrogen leaks can arise from a variety of sources such as damaged pipes, faulty valves/dispensers or failure of a shutdown mechanism. Hydrogen is typically stored at high pressures (300 - 950 bar) at hydrogen refuelling stations. Hydrogen is highly flammable in a wide concentration range (4-75% by volume in air) and has a relatively low auto-ignition temperature (520°C). Additionally, hydrogen releases can generate electrostatic charges that may lead to sparks, potentially triggering ignition.
Scenario
Hydrogen unloading procedure |
---|
This scenario involves a jet fire resulting from damage to a dispenser on one of the cylinders mounted on a tube trailer during hydrogen loading operations, leading to the release of highly pressurised gas. The associated project file uses a typical example of 350L cylinders on a tube trailer, each storing hydrogen at a pressure of 500 bar. |
Using the gas event tree for continuous releases, we can assess the possible loss of containment scenarios:
Jet Fire: The continuously released hydrogen will likely ignite due to its low ignition energy, either from friction or an external source.
VCE(Vapour Cloud Explosion): In the event of a continuous release of hydrogen that does not ignite immediately, a VCE can occur if ignition happens after the gas cloud has dispersed and finds a confinement.
Flash Fire: In the event of a continuous release of hydrogen that does not ignite immediately, a Flash Fire can occur if ignition happens after the gas cloud has dispersed and remains unconfined.
This case will focus on the consequences of a Jet Fire.
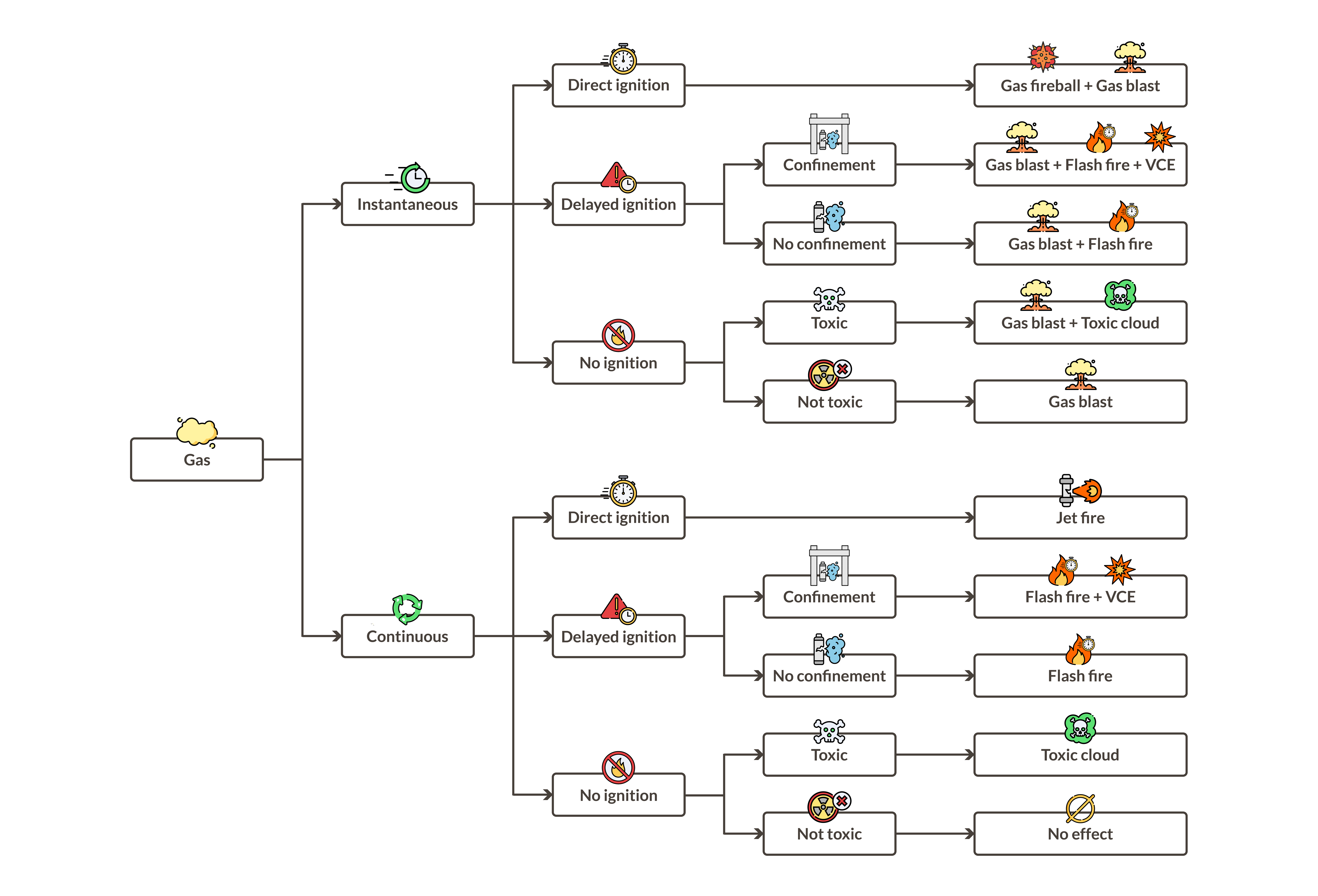
Gas Loss of Containment event tree
Modelling approach
To simulate the case, we start at the top of the tree and continue downward, filling in information node by node:
Add background. Define the context and environment for the simulation.
Add receivers (optional). Identify vulnerable areas or congested regions where flammable cloud dispersion might occur.
Add equipment. Set the location of the hydrogen storage tank on the map.
Select models. Start from the point of release and add subsequent models in the order of events to create a model tree.
Model selection
To model a Jet Fire event the ‘‘Jet Fire’’ model can be used. To determine the source condition for this model, the exit conditions of the hydrogen continuously leaking from the dispenser, the release model ‘‘Gas Release’’ may be applied. Alternatively, the whole chain of events can be simulated using the combined model ‘‘Gas LOC Scenario Continous Leak’’.
Source definition
Using an approach of modelling the order of events by linking models, the process starts with the ‘‘Gas Release’’ model to calculate the outflow conditions for the subsequent ‘‘Jet Fire’’ model.
Due to the negative Joule-Thomson effects, we use the isothermal expansion type for all hydrogen scenarios.
Model inputs for the Gas Release model:
Process Conditions |
|
Chemical name | HYDROGEN (DIPPR) |
---|---|
Initial temperature in vessel (°C) | 9 |
Initial (absolute) pressure in vessel (bar) | 500 |
Calculation Method |
|
Use which representative rate | First 20% average (flammable) |
Type of vessel outflow | Release through hole in vessel |
Type of release duration | Calculate until device is empty |
Expansion type | Isothermal |
Process Dimensions |
|
Vessel volume (m3) | 0,35 |
Hole diameter (mm) | 10 |
Hole rounding | Rounded edges |
Environment |
|
Ambient temperature (°C) | 9 |
Ambient pressure (bar) | 1,0151 |
Jet Fire
Subsequently, the Jet Fire model can be added. Linking the Jet Fire model to the release model automatically connects some of the source definition parameters.
The table below shows additionaly added input parameters, necessary for Jet Fire calculation.
‘‘Outflow angle in XZ plane’’ determines the tilt of the flame frustum.
‘‘Height of release’’ influences the vertical position of a Jet fire and, therefore the range of radiated heat.
Vulnerability settings define the translation method from heat radiation to damage level (lethality). The translation uses the Probit function, where the time of exposure is defined by the parameter ‘‘Maximum heat exposure duration’’ unless the scenario duration is shorter.
Process Dimensions |
|
Outflow angle in XZ plane (0°=horizontal; 90°=vertical) (deg) | 0 |
---|---|
Height of release (Z-coordinate) (m) | 1,5 |
Meteo Definition |
|
Meteorological data | Pasquill |
Pasquill stability class | C (Lightly Unstable) |
Wind speed at 10 m height (m/s) | 3 |
Predefined wind direction | W |
Vulnerability |
|
Maximum heat exposure duration (s) | 20 |
Take protective effects of clothing into account | No |
Heat radiation lethal damage Probit A ((sec*(W/m2)^n)) | -36,38 |
Heat radiation lethal damage Probit B | 2,56 |
Heat radiation damage Probit N | 1,3333 |
When linking subsequent events as models in EFFECTS, the models need to be organized in the order of events in a tree structure from top to bottom.
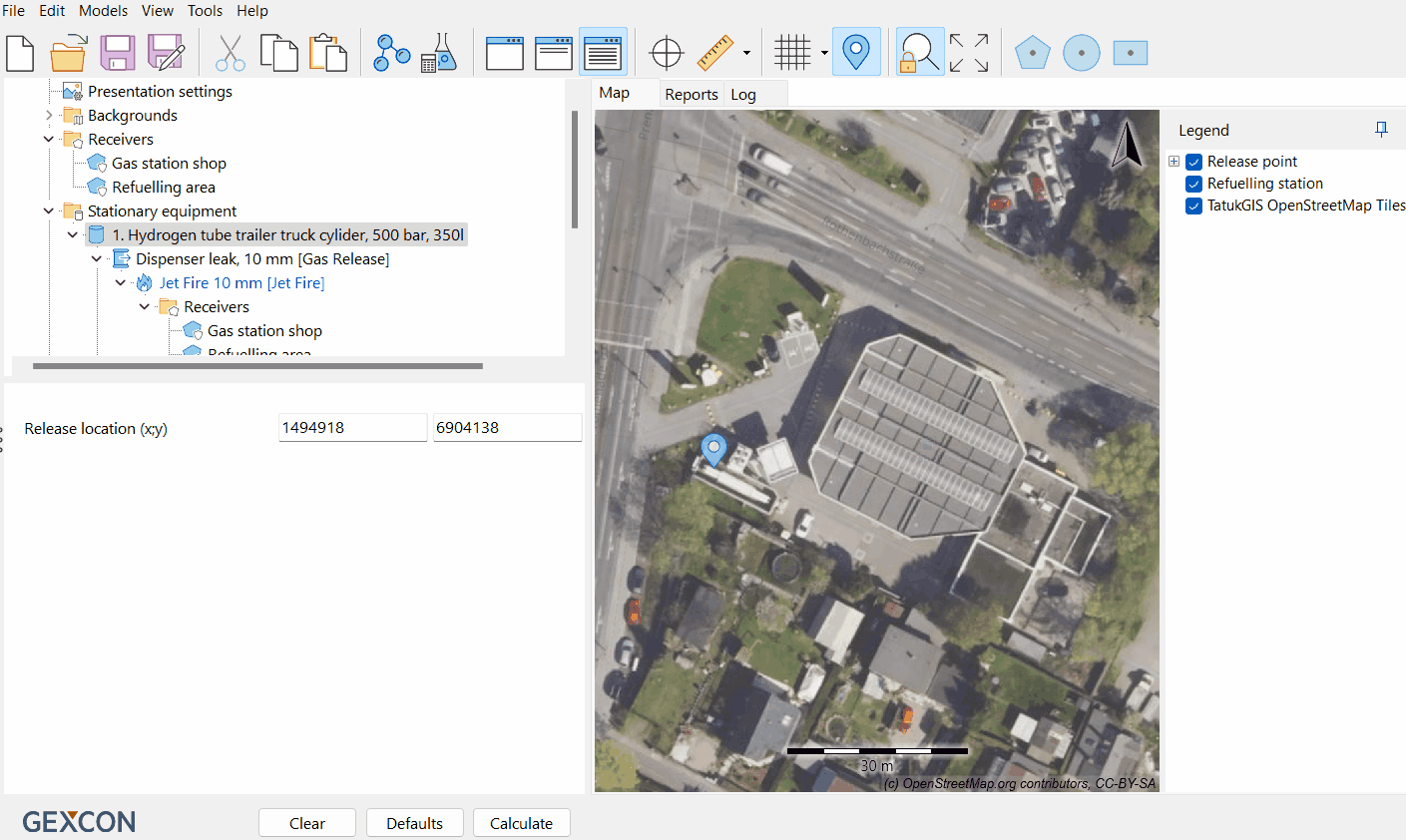
Linking release model, jet fire model and receivers
Using individual models and linking them usually provides more visibility in the selection of calculation methods. In this case, using an individual model does not offer any additional options compared to a combined model. While the combined model can run all possible scenarios, you can select to include only a Jet Fire, making both variants identical.
Results
The map visualisation shows the flame area, heat radiation contour and grid, and lethality contours. This data can be used to evaluate:
How far the jet fire will reach.
Expected heat radiation levels at different distances from the source.
Expected damage (burns) or lethality at various distances from the source.
Maps | |
Graphs | |
Reports |
Results can be customised by adjusting parameters such as contour levels, contour and grid colours, and combining graphs for a tailored analysis. For detailed guidance on adjusting and interpreting results, explore the presentation of results chapter. You can also export contours to Google Earth. Detailed steps are available in the article, How to export consequence results into Google Earth.
.png)
Influence of hole size on heat radiation dose from jet fire vs distance
Conclusion
Jet Fires and Vapor Cloud Explosions (VCE) are the most common concerns when handling pressurized hydrogen. The direct ignition of leaking hydrogen, resulting in a Jet Fire, can produce significant heat radiation, posing a danger to people near the release point and potentially causing domino effects. EFFECT assesses the consequences of a jet fire and helps determine the necessary safety distances for hydrogen operations.
Download the project file
Explore the project file simulating the jet fire at the refuelling station. Try to adjust the map contours, and select different graphs or multiple graphs at once (e.g., first, second, third-degree burns vs. distance). Evaluate how different hole sizes influence the received heat radiation dose by comparing results in a comparison set (picture below) and look into the receiver’s reports to assess the damage effect.
To view the project file, please open it using the EFFECTS software. If you don’t have the software, you can download and use the free viewing demo version of EFFECTS via the link below.
References:
1. RIVM. (2023). Calculation method for calculating the risks associated with the transport of compressed gases and cryogenic gases. Available at:https://rivm.openrepository.com/handle/10029/626793
2. NIPV. (2023.) Hydrogen filling station – Leak in buffer storage gas cloud explosion. Available at:https://scenarioboeken.nipv.nl/waterstoftankstation-lek-in-bufferopslag-gaswolkexplosie/